Task-Based Design and Policy Co-Optimization for Tendon-driven Underactuated Kinematic Chains
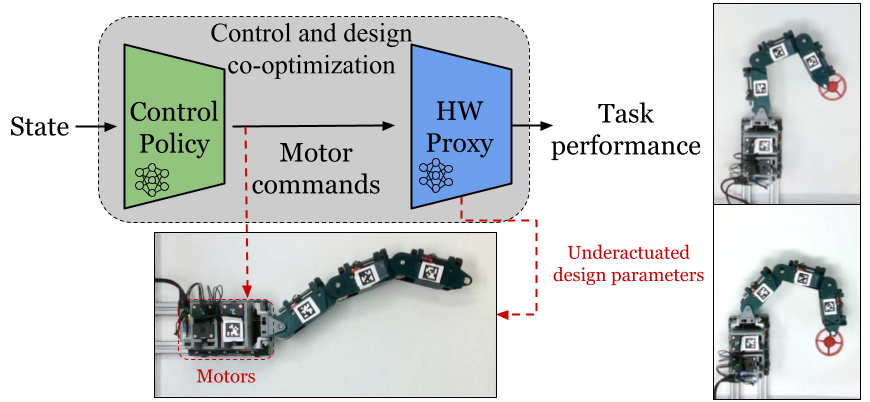
Underactuated manipulators reduce the number of bulky motors, thereby enabling compact and mechanically robust designs. However, fewer actuators than joints means that the manipulator can only access a specific manifold within the joint space, which is particular to a given hardware configuration and can be low-dimensional and/or discontinuous. Determining an appropriate set of hardware parameters for this class of mechanisms, therefore, is difficult - even for traditional taskbased co-optimization methods. In this paper, our goal is to implement a task-based design and policy co-optimization method for underactuated, tendon-driven manipulators. We first formulate a general model for an underactuated, tendon-driven transmission. We then use this model to co-optimize a three-link, two-actuator kinematic chain using reinforcement learning. We demonstrate that our optimized tendon transmission and control policy can be transferred reliably to physical hardware with real-world reaching experiments.
Paper
Latest version: Paper
Supplementary Video
Team
More real robot videos
Coming soon!BibTeX
TBD
Contact
If you have any questions, please feel free to contact Zhanpeng He